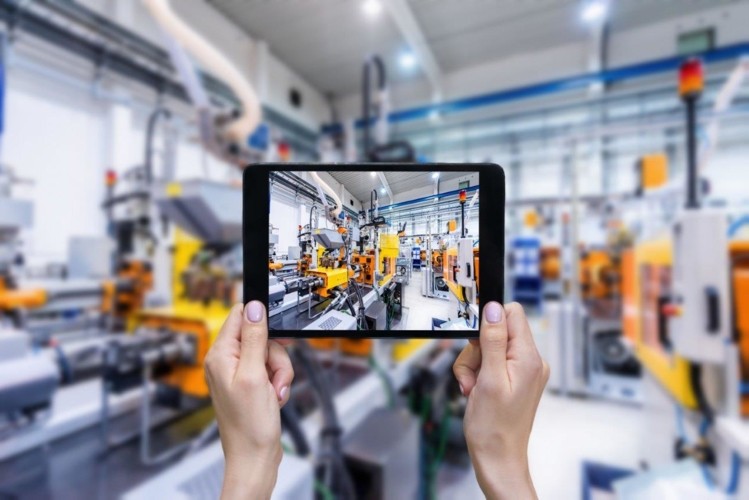
Have you wondered why more food plants aren’t engaged in Industry 4.0?
When the FPSA Technology Network came into being two years ago, the very first issue that the group started to address was the Industrial Internet of Things (IIOT) or what we are now referring to as Industry 4.0. While no one would ever accuse me of being technical, I became fascinated as I listened to our members over the next two years and started to understand the potential of this next generation technology for not just OEMs but especially for the food manufacturers where their equipment is in action.
As I have researched Industry 4.0, the first thing that becomes apparent is that different industries are utilizing it to much varied degrees. Some are all in while others are slow to adopt this technology. I’m afraid that the food and beverage industry, for the most part, falls into this latter category. In fact, having sat in on some of the Technology Networks calls, I knew that many of them were seeing much resistance to getting the remote access that they would need to generate the benefits of Industry 4.0.
This is supported in a piece I found online from Accenture titled, “Building More Value with Capital Projects”. While there is excellent data in this report, the results of one survey stood out. This is the impact of digital technologies/applications in recently completed capital projects among owner/operators. This highlighted the following.
Not Achieving Outcome | |
Reduced Operations & Maintenance Costs | 66% |
Construction Productivity | 62% |
On-time Completion Rate | 63% |
Improved Returns on Capital Employed | 64% |
Now, this survey was conducted across a variety of industries and did not target food and beverage. I’m afraid that if it had, the results might be even worse!
Maybe the food industry is a little too conservative to be an early adopter of Industry 4.0. Maybe suppliers just haven’t done a good enough explaining the benefits of Industry 4.0 to their customers.
As I dug into this issue, I discovered another perspective. In his interesting piece in Food Safety Tech, Brian Sharp pointed out the most obvious reason why we might be seeing hesitation in adopting Industry 4.0. How many food and beverage manufacturing facilities are over 50 years old and still utilizing legacy equipment? Those that work in the food industry are probably shaking their heads yes right now. But how do we rise above that?
As you read more and more about Industry 4.0, the benefits are clear. Tetra Pak has an excellent white paper that breaks these down very well:
- Increase Productivity via expanded and more efficient production
- Reduce Costs thanks to a continuous process of automation
- Respond More Quickly to the changing demands of customers
Going back to Brian’s piece, he captured this even better:
Getting the most out of operations is one of the most frequently cited needs of food and beverage manufacturers. The best way to do this is to drive plant efficiencies, which means measuring performance, setting baselines and goals, and holding employees accountable. The key here is to not confine efficiencies to just one area of the facility, but to broaden the scope to include end-to-end processes, from supplier to customer.
Frankly, these are some of the same goals I’ve been hearing about since I started over 20 years ago in this industry. It all makes so much sense but how do we get there?
One way is to focus on getting OEMs and manufacturers at the same table to discuss this important topic. For food and beverage manufacturers interested in being a part of this discussion, we have developed a brief survey to solicit your feedback. In addition, if you would like to participate on our Industry 4.0 Task Force to contribute to a deeper understanding of this topic and help us move it along, please feel free to email me at your convenience.
Andy Drennan
SVP, Membership and Business Development
Food Processing Suppliers Association