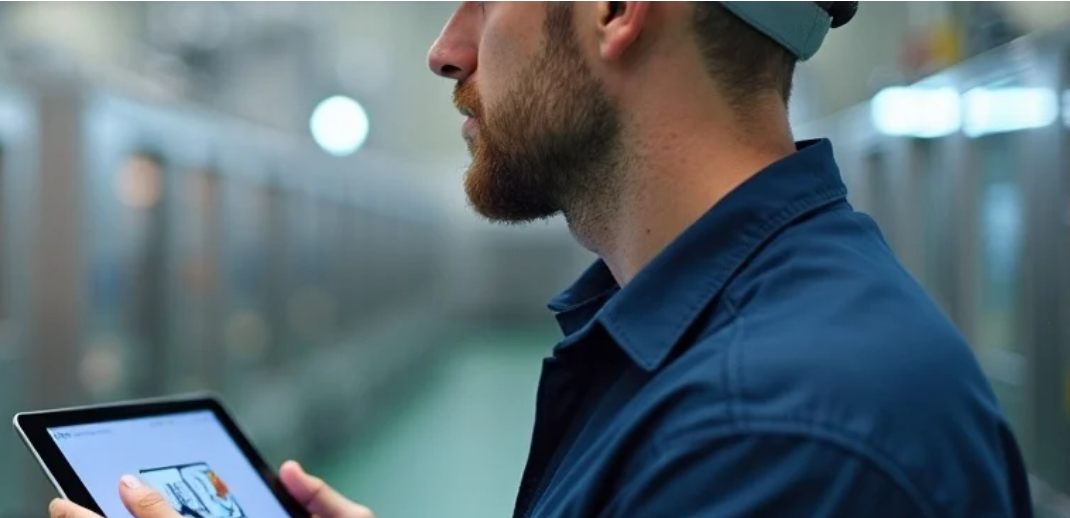
Alex Ball | Original Post
Operational success is more than robust food safety protocols; it's a workforce that is flexible, resilient, and knowledgeable across multiple domains.
In food manufacturing, food safety often dominates conversations—and rightfully so. Ensuring the safety of consumable products is non-negotiable. However, operational success in this industry demands more than robust food safety protocols; it requires a workforce that is flexible, resilient, and knowledgeable across multiple domains. This is where cross-training becomes a game-changer.
The Advantages of Cross-Training in Food Manufacturing
- Operational Flexibility
In a fast-paced manufacturing environment, unexpected challenges like equipment breakdowns, staffing shortages, or seasonal surges are inevitable. Cross-trained employees can step into multiple roles, ensuring that production lines keep running and deadlines are met without compromising quality or safety.
- Strengthened Maintenance Practices
While food safety is a critical priority, equipment maintenance is its indispensable counterpart. Cross-training employees in maintenance practices equips them to proactively identify and address potential mechanical issues before they escalate. Operators who understand basic maintenance fundamentals can troubleshoot minor issues, reduce downtime, and prevent costly disruptions. A well-maintained production line ensures operational continuity and upholds food safety by minimizing biological and foreign material contamination risks stemming from faulty equipment.
- Enhanced Food Safety Compliance
Cross-training expands employees’ understanding of how their roles intersect with food safety standards. For instance, teaching machine operators about sanitation practices helps them recognize potential hazards and address them proactively. This comprehensive awareness strengthens your facility’s compliance and reduces the risk of contamination.
- Employee Engagement and Retention
Employees who are given opportunities to learn and grow tend to be more engaged and satisfied in their roles. Cross-training not only broadens their skill sets but also makes their work more dynamic and meaningful. Engaged employees are less likely to leave, which is a significant advantage in an industry often plagued by high turnover rates, and an aging workforce.
- Knowledge Redundancy
Relying on a single employee to be the expert in a specific area creates vulnerability. If that person is unavailable, critical processes can stall. Cross-training builds knowledge redundancy, ensuring that expertise is distributed across your workforce.
How to Implement Cross-Training in Your Facility
Start with a Skills Assessment
Identify the core competencies required for each role in your facility and evaluate the current skill levels of your employees. This will help you pinpoint gaps and opportunities for cross-training.
Prioritize Safety and Maintenance
Ensure that cross-training initiatives incorporate food safety, maintenance, regulatory requirements, and foundational GMP skills. Employees must understand how their new skills align with maintaining both a safe production environment and reliable equipment performance.
Use Structured Approaches
Incorporate structured learning and development programs that provide consistent, accessible, and trackable training modules for employees. Interactive digital courses, simulations, and video tutorials can complement hands-on experiences, ensuring employees grasp concepts before applying them in real-world scenarios. Pair these programs with on-the-job practice and shadowing opportunities to reinforce skills and promote knowledge retention.
Monitor and Evaluate Progress
Regularly assess the effectiveness of your cross-training program. Solicit feedback from employees, measure improvements in operational metrics, and refine your approach as needed.
Realizing the Full Potential of Cross-Training
Cross-training isn’t just a workforce strategy; it’s a culture shift. When employees understand how their roles contribute to the broader operational and safety goals of the organization, they become more invested in the success of your operations. Beyond enhancing food safety and efficiency, cross-training fosters more well-rounded employees, a sense of teamwork, and shared responsibility that is invaluable in today’s competitive market.
Food safety may be the cornerstone of your operations, but operational success is built on a foundation of adaptability and resilience. By investing in cross-training—including a strong focus on maintenance training—you’re not just preparing your workforce for today’s challenges; you’re equipping them to thrive in the face of tomorrow’s uncertainties.