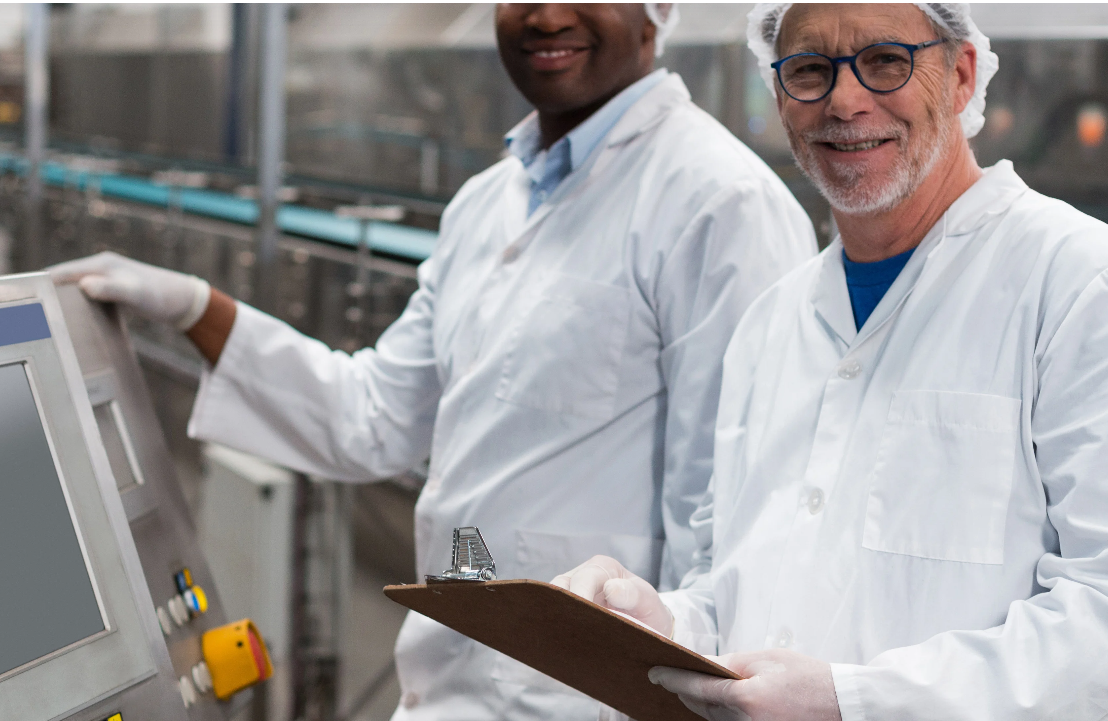
A comprehensive guide to fostering a safety-first culture for operational excellence.
Investing in equipment for a food production facility is a significant decision that requires strategic planning. The cost of these machines commonly ranges between $150,000 to $500,000 for any new machinery or equipment used for food processing and packaging.1 While technology and automation have created significant value from these machines, ensuring the safety of the people running and operating the machine is a critical factor in increasing output.
Ineffective training, inconsistent standard operating procedures, and low accountability around complex machinery can lead to significant safety incidents, and equipment failures, and cause significant downtime costs. Food Processing Magazine reports that a single hour of machine downtime can cost a facility an astounding $30,000 per hour, not including maintenance expenses.2 To minimize unforeseen expenses and maximize productivity, it’s essential to prioritize safety, invest in training, and optimize procedures around your equipment. Here’s a comprehensive guide to creating a safety-first culture to protect your equipment investments:
1. Invest in Accurate and Comprehensive Safety Training
Safety comes first. When you move someone to a new piece of equipment, be certain they have had the necessary safety training. If you move people from machine to machine, each may be very different and require different education on its proper use and maintenance. Knowledge and comprehension of all aspects of equipment operation, maintenance, and safety procedures should not be overlooked so your team has confidence in their ability to operate and maintain the machines efficiently.
- Make Training Engaging and Comprehensive: Instruct your employees on correctly doing their job(s) through visual, engaging, and innovative training that appeals to a diverse audience. For the quickest path to proficiency, video-based training can capture your exact operation and train on a proprietary piece of equipment, for a specialized role, or on any subject matter that needs a repeatable training process that captures exactly how you imagine it. Offer training in multiple languages and include interactive quizzes that test retention to increase proficiency significantly. This can also reduce the future risk of OSHA recordables and related workers’ compensation legal expenses.
- Ensure Easy Access to Training: Utilize QR codes to easily link to mobile training materials where employees can quickly learn what they need to know about a specific machine. Consider training that is available on multiple devices so learners can jump in at any time and from anywhere.
- Provide Regular Refreshers: Schedule training updates to ensure your team is confident, compliant, and competent. Consider a platform that can automatically enroll employees in training based on job role, code, department, location, or line and where training content can be reassigned as frequently as needed for auditing and compliance purposes. Especially for important safety content like Lock Out-Tag Out procedures.
2. Safety First for Your People
Employee safety is a top priority in any production facility. Employees want to trust that their leaders and employer will create an environment to keep them safe. Invest in implementing robust safety measures to protect both your equipment and your operators.
- Protect Your People: Install basic safety measures on your machines like machine guards, barriers, eStops, and Lock Out-Tag Out to prevent incidents. Personal protective equipment (PPE) is your employee’s first line of defense against injury. Mandating proper PPE and training your people on how to correctly use PPE for the job task is a low-cost way to save you big money in the long run.
- Don’t Forget Ergonomics: Ergonomics is a vital part of workplace safety in manufacturing. This is highly important to protect people from both acute self-injury and long-term injuries. Ergonomic solutions and training can make employees more comfortable, safe, and increase productivity.
- Try Micro-Modules: Health and safety courses can be delivered quickly and efficiently in micro-module formats. Available in multiple languages, these courses can be completed in 5-10 minutes, allowing learners more flexibility and faster skill acquisition.
3. Implement Consistent Standard Operating Procedures (SOPs) Across Every Plant and Shift
Continuity and consistency across facilities, departments, and shifts are critical. SOPs are essential to ensure consistent and correct operation of your machines. Develop detailed SOPs for every piece of equipment and ensure they are easily accessible to all employees, at every plant.
- Document. Document. Document: In daily huddle meetings, address safety first. Utilize a simple documenting tool like a safety cross to create safety systems and protocols that will help safeguard employees and hold teams accountable. It’s also important to carefully organize and track your team’s training acknowledgment forms and monitor employee education to know these records are safe and accurate. Store your training acknowledgment forms electronically to ensure records are easily accessible and organized for audit readiness purposes.
- Provide Step-by-Step Instructions: Provide clear, step-by-step instructions for operating and maintaining each piece of equipment. Consider having live training videos created that demonstrate the correct procedures and behaviors expected within the specific work environment. This modeling is crucial for setting standards and expectations, providing a clear example for learners to emulate, which can lead to more consistent performance and adherence to safety protocols.
- Regularly Review Content and Accessibility: Regularly review and update SOPs to reflect any changes in equipment or processes. Ensure SOPs are readily available at the point of use, either in printed form or digitally.
4. Foster a Culture of Maintenance Accountability
Encourage a culture of accountability in your workforce. When employees understand the importance of their role in maintaining equipment, they are more likely to follow procedures diligently.
- Set Clear Responsibilities: Define and communicate the responsibilities of each team member regarding equipment handling and maintenance.
- Reward Compliance: Recognize and reward employees and teams who consistently adhere to safety and operational guidelines. If they have a long streak of weeks with no reported safety incidents, celebrate it!
- Promote Continuous Improvement: Promote a culture of continuous improvement where learning and development are encouraged. Utilize a solution offering career pathways where employees can become well-rounded and advance their professional education from entry-level learner to leader. This allows you to easily provide clear and consistent development paths for re-skilling and up-skilling your workers.
5. Regular Maintenance and Inspections for Your Machines
Routine maintenance and inspections are essential to keep equipment in optimal condition and prevent unexpected breakdowns. Regular maintenance checks provide reassurance of continued machinery performance, and an opportunity for new software updates, reviewing safety systems, checking of guarding, and more. Develop a maintenance schedule and adhere to it strictly.
- Preventive Maintenance: Perform regular maintenance checks to identify and fix potential issues before they escalate.
- Inspection Logs: Maintain detailed logs of all inspections and maintenance activities.
- Professional Servicing: Engage professional technicians for complex maintenance tasks and ensure they are certified.
Conclusion
Prioritizing safety for your teams is an ongoing process that requires attention to detail, continuous training, and daily dedication. By creating a safety-first culture for your team, operational excellence and a return on your equipment investments will soon follow. Ultimately, a safe facility protects your capital investments and fosters a more positive and higher-quality environment for your employees.
Sources:
- “Food Manufacturing Startup Costs,” FinModelsLab, from July 2024.
- “Reducing Food Processing Plant Downtime,” Processing Magazine, from March 2021.