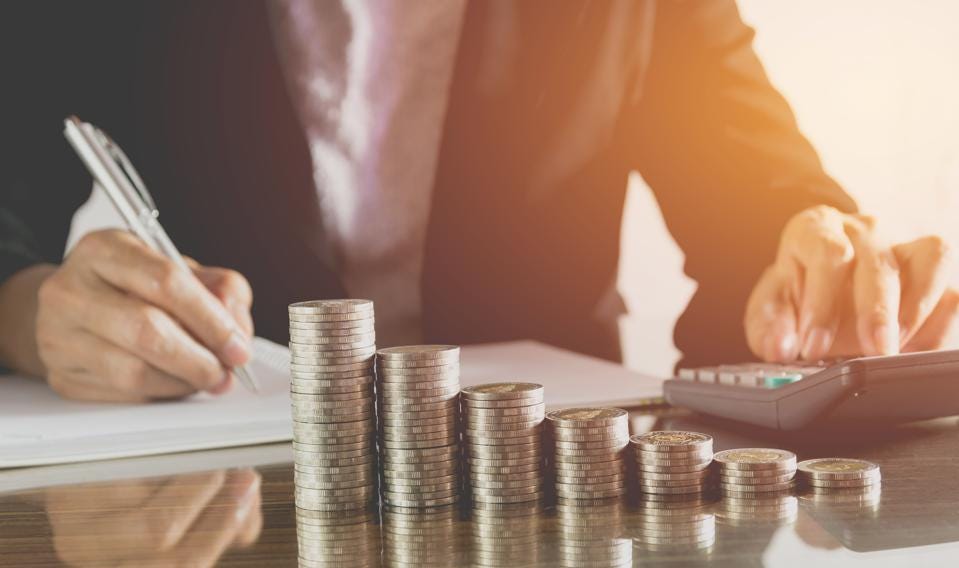
This morning, I read a piece on investments in the food industry from a panel at the Future Food-Tech Conference held last week in San Francisco. According to panelists, with investments into food industry technology doubling in 2021 to $13.8B, there is still much room for additional investment as cutting-edge technology is required to explore new opportunities in the food and beverage segments. One panelist even estimated that in the category of alternative proteins alone, another trillion dollars-worth of infrastructure needs to be built to meet the demand that exists.
While I absolutely understand the need for this investment, I’m more concerned about the day-to-day operations and what it takes to get product out the door TODAY and into the retail supply chain. I’m referring to service technicians in the plant or with the OEMs, and more importantly the growing need for all of us to recruit young people into these roles. This was a problem even before the pandemic, but now with many baby-boomers having opted to retire, the situation has become critical.
According to a pre-pandemic survey conducted to nearly 40,000 employers in Europe back in 2018, 70% of service organizations claimed that they will be burdened by a retiring workforce within 5 to 10 years. Let’s see, that was four years ago and prior to a pandemic that would take many older workers out of the workforce. I don’t think you need to be Nostradamus to see that the situation is even worse now than it was when the results for that survey was written.
Perhaps this is why the FIT (Food Industry Technician) Certification program is taking off and after only a few short years, is undergoing a radical expansion of its campus and class sizes. Students at the Indianapolis campus of Lincoln Tech are watching as their classmates go into the program, and within months are fielding excellent job offers from both food processing CPG firms and their equipment suppliers. Results so far are extremely promising, thanks in large part to the hands-on training these students receive on actual equipment donated from many of the food industry’s bellwether OEM’s. Additionally, these courses are supported by many of the same OEMs who send staff in to talk with the students with the goal of helping them to better understand what a career in the food industry is like and what type of opportunities are out there for them.
Even with the expansion of the FIT program this quarter, it’s going to take a lot more work to truly address this workforce shortage. As FPSA looks to continue growing this program and further expand the classes, we’ll have to keep one eye out for the future. More campuses? More students and teachers? More equipment donations? Check, check and check. It’s all on the table.
I agree with the panel in San Francisco and will be interested in watching how investment flows into the industry for new products and categories. However, even when that investment comes online and is ready to start delivering finished product, who will be there to maintain the equipment? When that day comes, I won’t be surprised to learn that person comes with a FIT certificate.
Any equipment manufacturer or food processor interested in learning more about getting involved in the program should reach out to FPSA President, David Seckman (dseckman@fpsa.org).
Andy Drennan, FPSA SVP