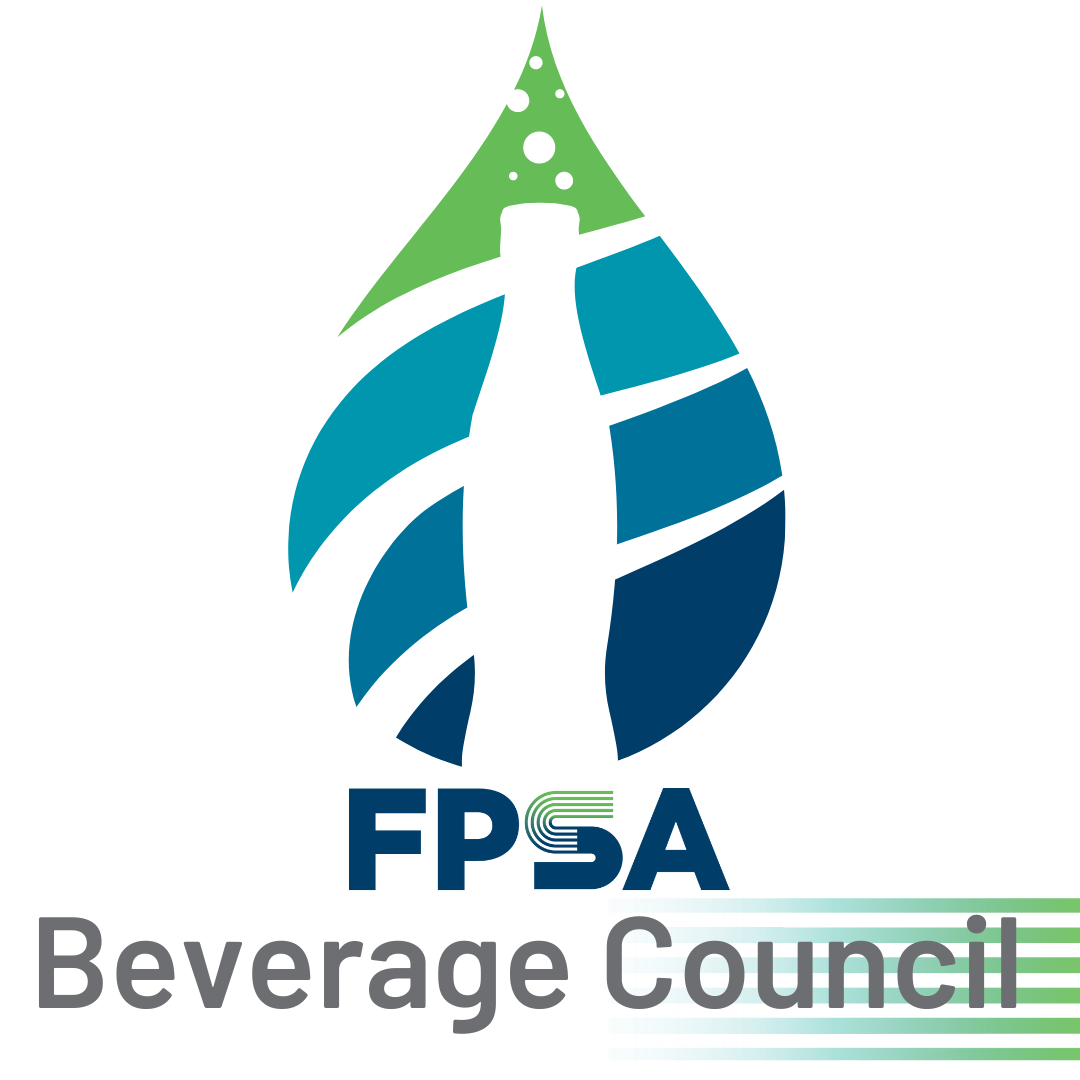
In today's competitive beverage industry, efficiency and sustainability are more crucial than ever. The FPSA Beverage Council has identified innovative ways for beverage producers to maximize their product yield during the filling process. By leveraging advanced technologies such as precision filling systems and lean manufacturing principles, companies can significantly reduce waste, save costs, and build customer loyalty.
Precision Filling Technologies
Accurate Filling Systems: Precision is paramount in the filling process. Leading FPSA member companies like Krones, JBT, Fogg Filler, and GEA provide cutting-edge filling systems that ensure each bottle or can is filled to the specified amount. Some systems use load cells to control fill quantities precisely, preventing overfilling and spillage. This not only saves products but also upholds the high hygiene standards crucial for beverages, giving producers confidence in the quality of their products.
Minimizing Waste: Product loss is difficult to quantify, with overall machine operating efficiency (OEE) typically exceeding 96.5%. It largely depends on factors such as bottle integrity, fill speed, fill height, and the design expertise of filling vendors in areas like changing parts, bottle pockets, transfer ratios, and starwheel sizes. These advanced systems are critical in reducing product loss, particularly during product changeovers, where many customers aim to minimize loss to less than 100 liters.
The efficiency of these systems, backed by advanced technology, also translates to less frequent maintenance and downtime, further boosting productivity and ensuring product quality.
Lean Manufacturing Principles
Applying Lean to Beverage Production: Originally developed in the auto industry, lean manufacturing principles are revolutionizing the beverage sector. Lean manufacturing maximizes value while minimizing waste. By identifying and eliminating non-value-adding activities, beverage producers can significantly streamline their processes, gaining a strategic advantage through enhanced operations.
Five Core Lean Principles:
- Identify Value: Understand what creates value for the customer and focus efforts on enhancing these aspects.
- Map the Value Stream: Create a visual representation of the production process to identify and eliminate waste.
- Create Flow: Design continuous workflow processes to avoid interruptions and idle time.
- Establish Pull: Produce based on customer demand to avoid overproduction.
- Seek Perfection: Engage in continuous improvement to refine processes incrementally.
Environmental and Economic Benefits
Sustainability: Implementing precision filling and lean manufacturing conserves resources and supports sustainability goals. Efficient use of water, energy, and raw materials reduces beverage production's environmental footprint.
Economic Gains: Reduced waste, especially during product changeovers, results in significant cost savings, which can be reinvested in promotional activities, such as product giveaways. Offering free samples to customers can foster loyalty and increase sales, creating a beneficial cycle for the business.
Building Customer Loyalty
Promotional Giveaways: Beverage manufacturers can afford to give away some products by saving them through efficient processes. This practice helps with marketing while also strengthening customer loyalty. Satisfied customers are more likely to return, creating a loyal customer base to drive long-term success.
– Elena Sierra, FPSA, on behalf of the FPSA Beverage Council
Learn More About FPSA Beverage Council