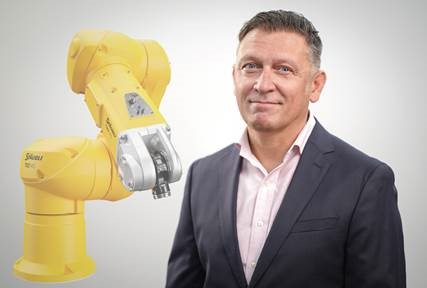
For months, I have been meaning to bring up the Production Lines at PROCESS EXPO last November. These three working lines brought together 27 different manufacturers to produce gluten free focaccia rolls, plant-based chicken nuggets and frozen packaged meatballs in demonstrations throughout the day that highlighted the latest innovations in processing and packaging technology. I must admit, overseeing the production line program is one of my favorite tasks as I get to, not only see this equipment up close and personal but to work with some of the professionals that manufacture it.
One piece of equipment that I was particularly impressed by was the Stäubli robot arms that were utilized in conjunction with EnSight Solution’s palletizer in the Meatball Production Line.
In late December it was my pleasure to discuss the company and its technology with Stäubli Head of Business – General Industry & Food, Gilles Le Quilleuc.
FPSA: Gilles, people were fascinated with Stäubli’s robotics in the Production Line. Can you tell me which model was used and how long this particular model has been on the market?
The model used in the production line was the TX2-160L. This robot was launched this year and it is the new generation of Stäubli robot TX2 series, helping customers to increase their productivity. Frankly, this arm is the perfect robot for collaborative palletizing in primary processing and in secondary packaging in food applications. This arm can carry up to 80 lbs with a very fast cycle time (productivity) in a safe environment. With a safety level of PLe/SIL3 for all functions, it’s unique and does not have an equivalent on the robotics market.
FPSA: As I’m sure you know, a food production plant can be an unforgiving environment. How does the TX2-160L handle these challenges?
Yes, you are correct about that. However, Stäubli equipment has been handling these challenges for about 20 years with HE (Hygienic Environment) compatible models of its equipment. This model is available to work in any food processing environment and resist all cleaning procedures, making it unique in the robotics world.
FPSA: Material handling has been one of the early adopters to robotics in the food plant. How do you see this trend evolving?
With workforce issues and concern for employee safety due to COVID19, food processors are investing in robotics because they need it just to get product out the door. Stäubli understood this many years ago, and that’s why we focused on food processing applications in harsh environments going back to 2001, back when most suppliers were still just focused on material handling.
FPSA: Does Stäubli produce technologies for further upstream, for example in food processing?
We are working on a variety of applications in different categories and have been for about 20 years. For example, we are focusing on slicing curds and palletizing in Dairy; on cutting/deboning to palletizing in Proteins. Other examples include chicken deboning, waterjet cutting, harvesting, and breading. Given the workforce shortages our customers are seeing, all these operations might benefit from robotics.
FPSA: What are some of the challenges you have seen among customers in adopting robotic technologies?
The main challenge is time. Many customers take up to a year or two to before convinced of the benefits of adopting and implementing robotics for the processing application. That is, for the first robot they purchase. Once complete, the second purchase comes soon after, maybe even just a few weeks because the benefit is obvious. It’s normal that they want to understand how this technology can be applied in their plant and that they are using the best robot, have adequate support for it and that this robot is able to resist this harsh environment. For this reason, we explain that Stäubli is not a start-up. With 130 years in the market, Stäubli has the experience to provide excellent machinery and support for it.
FPSA: Talk to me about food safety. How does food safety fit with your robots?
We introduced our HE robot in food processing applications 20 years ago for one good reason, our customers asked for it. These customers saw the range of our cleanroom robots designed for the semiconductors over 35 years ago and asked us to apply this technology in their plants due to the clean design of our robots. At this time Stäubli was the only robot manufacturer supplying robots with a closed structure (all cable and motors covered). We understood quickly that our robots were well suited for the CR environment (low temperature, humidity, washdown) and could keep the finished product (food) safe for consumers. Just like any supplier to the food industry, safety is our number one concern (no accidental contamination with food grade oil), coupled with performance and reliability (resistant to washdown procedures) and for this reason, we designed our HE* robot according to EHEDG (European Hygienic Engineering & design Group) directives beginning in 2007.
FPSA: I worked on a panel session at Process Expo where the panelists spoke about workforce shortages pushing food processors into much higher degrees of automation just to get product out the door. Has that been Stäubli’s experience and if so, do you see us ever getting back to the pre-COVID levels of reduced automation? In short, is this increased level of automation here to stay?
Frankly, I think the level of Automation will continue to increase and perhaps much more so than today. As you mention, there is a serious workforce shortage and that is not going away. Some workers are afraid to work in these conditions during the pandemic for very simple reasons. Not only is there risk of getting ill but it is also hard work. For example, in my family I had 2 uncles who worked as butcher/deboners in a protein plant. It was a very hard job that I don’t see the next generation stepping up to do this type of work. Maybe they prefer to work in computer science or other service industries. This workforce problem for the food industry is only just beginning. Processors will have more difficulty finding people for production, while the demand for their products will only continue to grow. This is simple demographics. Increasing automation is the only way to deal with it.
FPSA: For that food processor out there reading this, who knows they need to increase their automation to ensure consistent production, what are some of the first things they need to think about before bringing in a company like Stäubli?
Many plants and machines have been built for manual operations and the production flows and footprint are designed as such. This is the main problem they must address before automating the plant. It is critical to rethink the flows to prepare the best layout for this automation to truly take advantage of the efficiencies of this technology. Once done, you can best design the production lines and implement automation and robotics for optimum results.
FPSA: Gilles, this has been very helpful. Thank you.
Andy Drennan, FPSA SVP