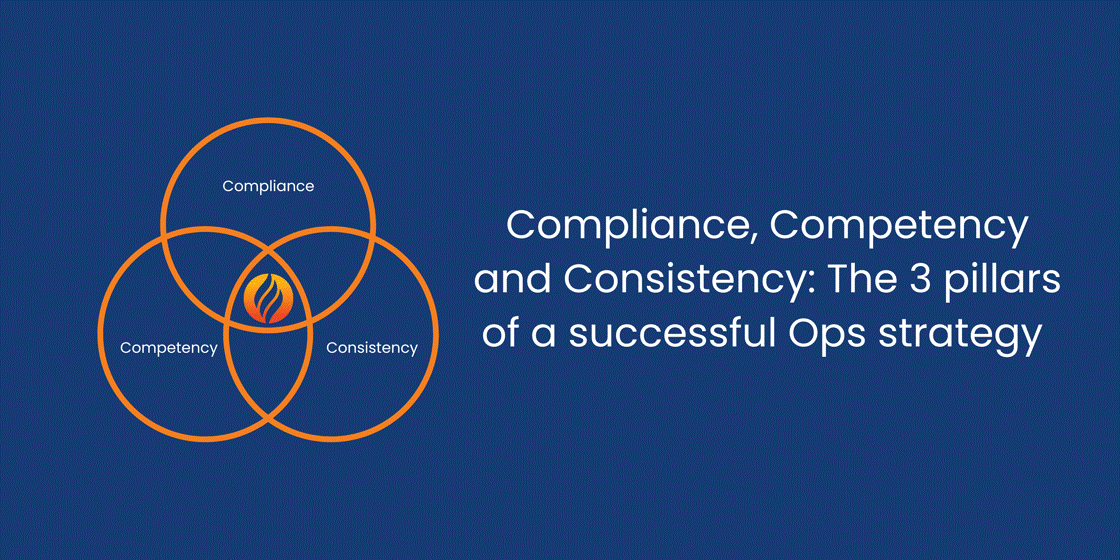
Peak performance in food production requires a training and development culture that embraces the three C’s: Compliance, Competency, and Consistency.
Creating a consistent, quality product at scale while managing cost is no simple task. It’s made more complex with high turnover, recruitment challenges, inconsistencies in training across plants and seismic shifts in the workforce coming.
Additionally, there’s concerns over substantial risk to your brand and bottom line if a recall or work stoppage were to occur. For food production operators, you must safeguard your operations against all these things. One simple area of focus is how well you train and develop your production workers.
Investing in people, especially front-line employees, is not just a matter of regulatory compliance; it’s a strategic-level imperative that drives performance. The key to unlocking this potential lies in establishing a training and development culture that embraces the three C’s of food production: Compliance, Competency, and Consistency.
Compliance: The Foundation of Trust and Safety
Compliance with food safety regulations and industry standards is the cornerstone of any food production operation. It ensures that products are safe for consumption and that the company adheres to legal requirements, avoiding costly fines, repetitional damage, product loss and ensures employee safety.
Why Compliance Matters:
- Regulatory Adherence: Meeting the stringent requirements set by bodies such as the FDA, USDA
- Audit Preparedness:Audits can be substantial drains on productivity, but do not have to be. Digital training records for all training ensure limited disruptions and the ability to demonstrate a systematic approach to training and documentation.
- Risk Management: Reducing the likelihood of foodborne illnesses, recalls, and the associated financial and reputational costs.
- Consumer Trust: Building and maintaining trust with consumers by ensuring product safety and quality.
Investing in training programs that focus on compliance helps employees understand the critical importance of these regulations and equips them with the knowledge to implement best practices consistently, most importantly you keep your customers and employees safe.
Competency: Building a Skilled Workforce
Compliance is incredibly important, but it’s also the bare minimum. Competency is about developing a skilled and knowledgeable workforce capable of performing their tasks efficiently and effectively. Competency-based training programs focus on developing the specific skills and abilities that employees need to excel in their current roles, while developing more advanced skills for their next role.
Why Competency Matters:
- Efficiency and Productivity: Skilled employees can perform their tasks more efficiently, reducing waste and increasing productivity.
- Innovation and Improvement: A competent workforce is better equipped to contribute to continuous improvement initiatives and innovative solutions.
- Employee Engagement:Providing opportunities for skill development enhances job satisfaction, retention and reduces turnover rates.
- Better and ongoing training means more versatility: Call-ins and turnover will always be a challenge. Creating a versatile team will enable you to adjust staffing with ease to avoid costly shutdowns.
By investing in competency-based training, COOs can ensure that their teams are not just compliant but also driving higher performance and enhancing your bottom-line.
Consistency: The Key to Sustained Performance
Consistency in processes and practices is essential for maintaining high performance levels in food production. Consistent training ensures that all employees are on the same page, following the same procedures and standards, which leads to more predictable and reliable outcomes across shifts and plants.
Why Consistency Matters:
- Standardization: Uniformity in processes reduces variability, ensuring that products meet the same quality standards every time.
- Continuous Improvement: Consistent training programs allow for the ongoing refinement of processes based on feedback and performance data.
- Scalability: As the company grows, consistent training ensures that new employees can be onboarded and integrated smoothly, maintaining performance standards across the board.
- Succession Planning: Consistency is not limited to process, but also to passing down knowledge. As the Baby Boomer Generation begins to hit retirement age, it is imperative that processes be documented and well trained to not lose decades of experience.
By fostering a culture of consistency through regular and standardized training programs, COOs can ensure that their operations run smoothly and efficiently, regardless of external pressures or changes.
In a competitive industry where margins are often tight and the cost of failure is high, the strategic investment in training is not just an option—it’s a necessity. Embrace the three C’s formula and unlock the full potential of your workforce, ensuring that your company remains at the forefront of the food production industry.